

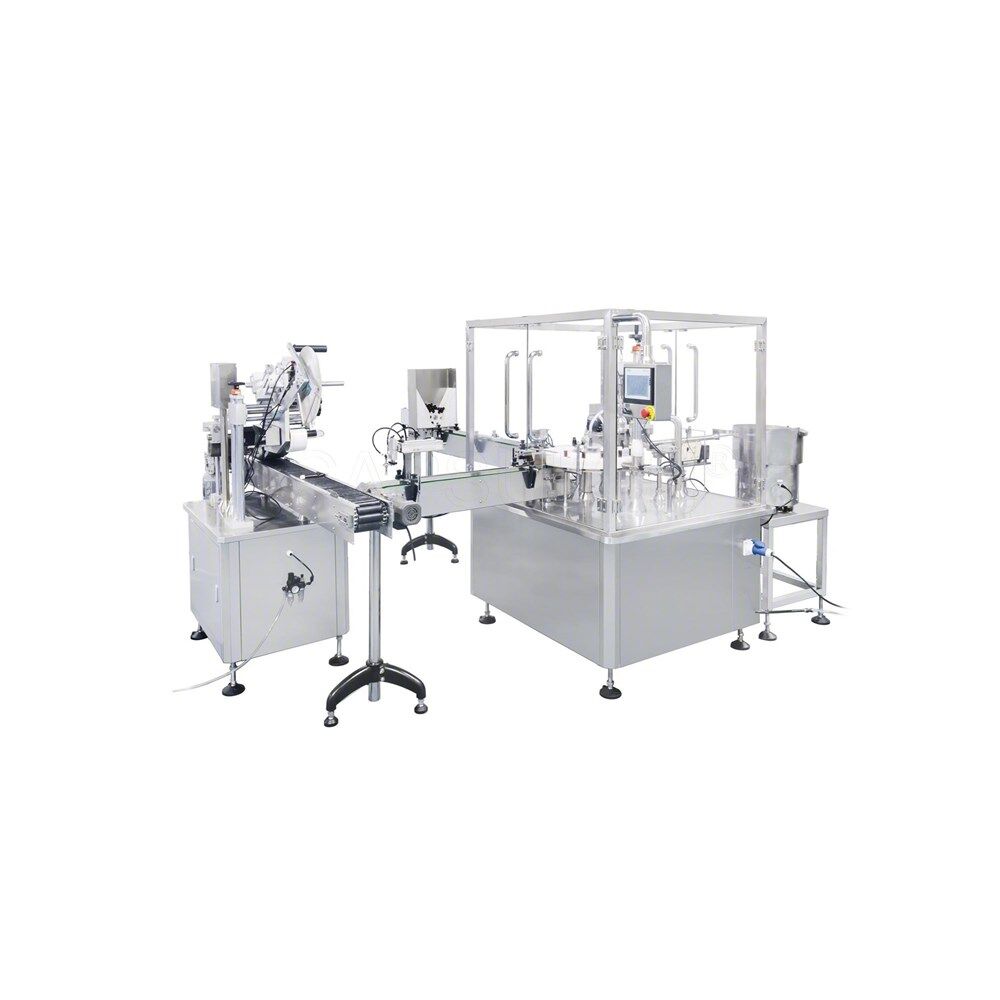
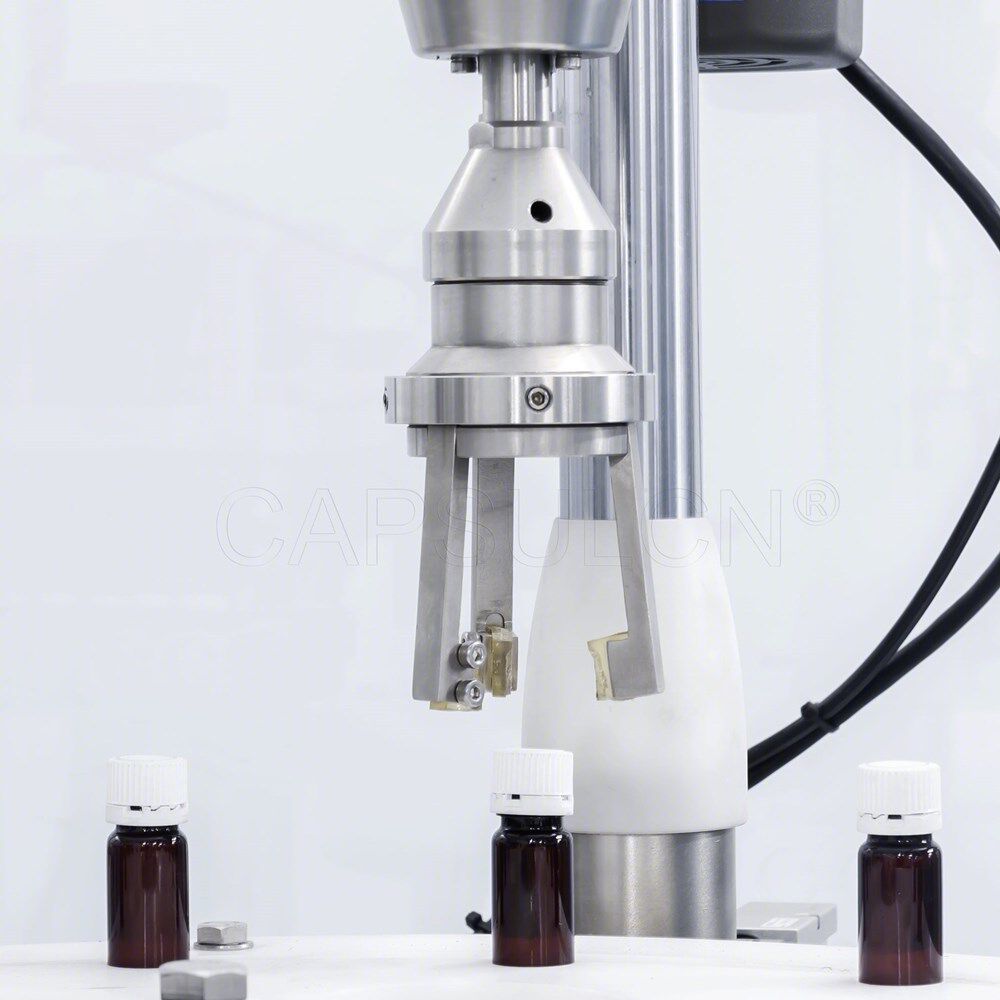
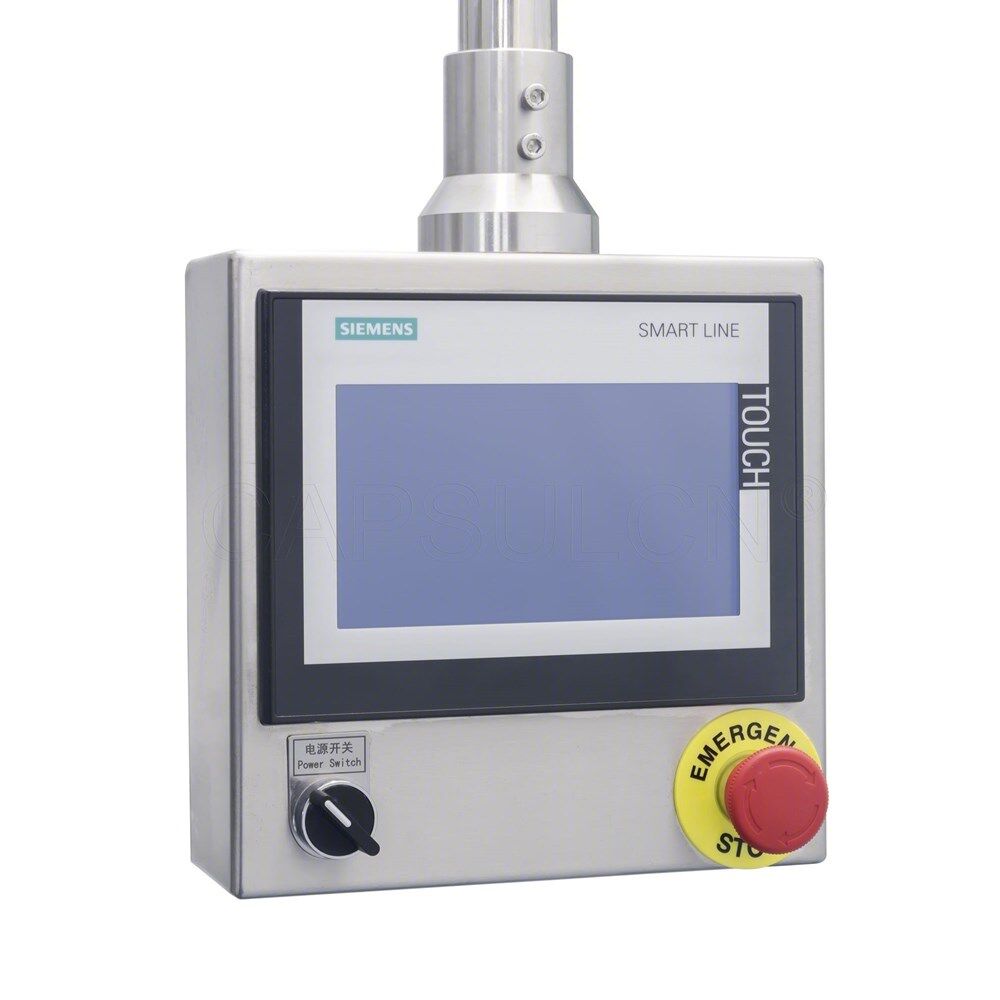
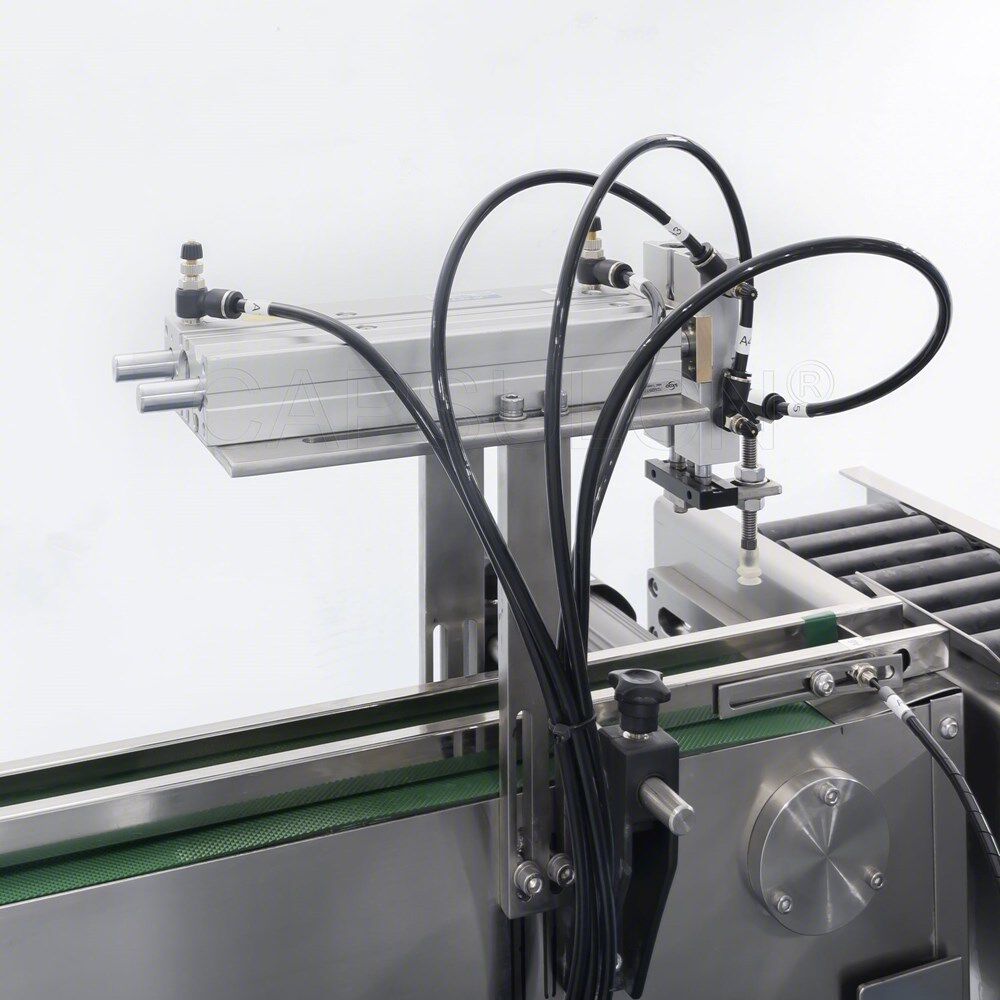
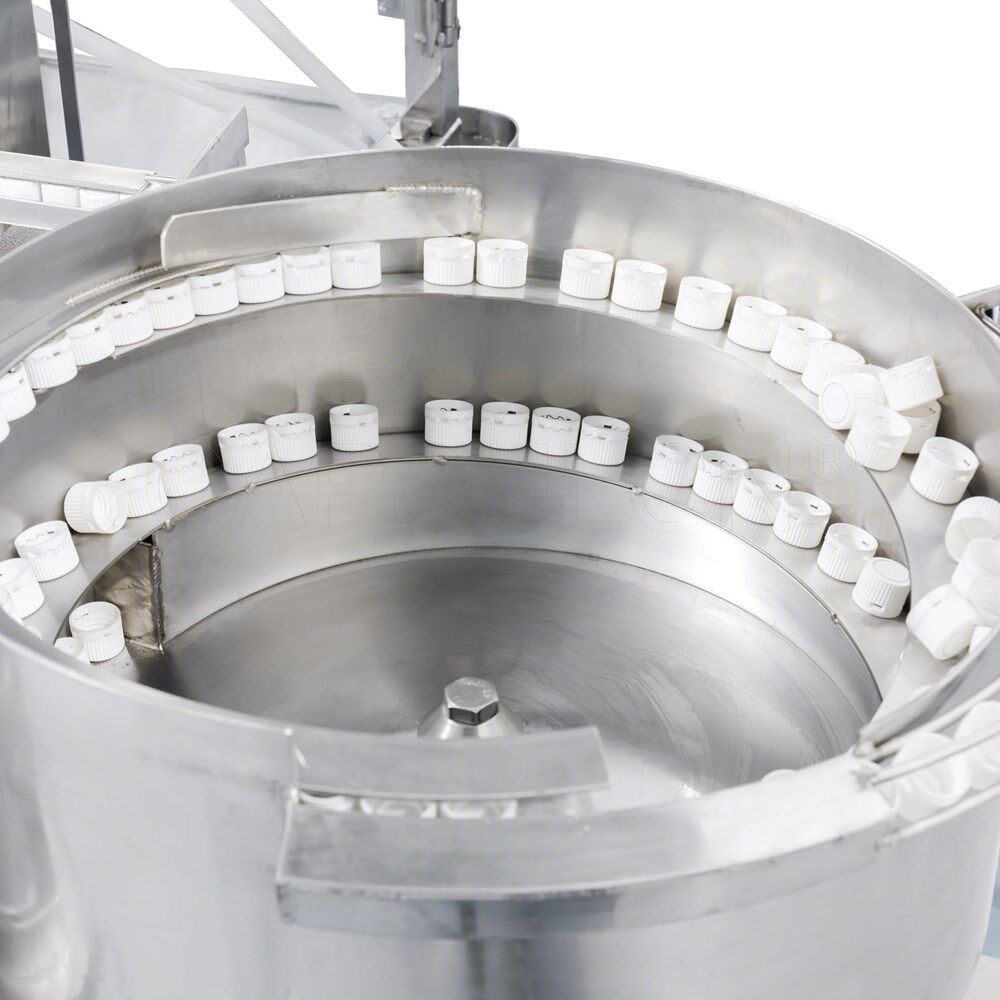
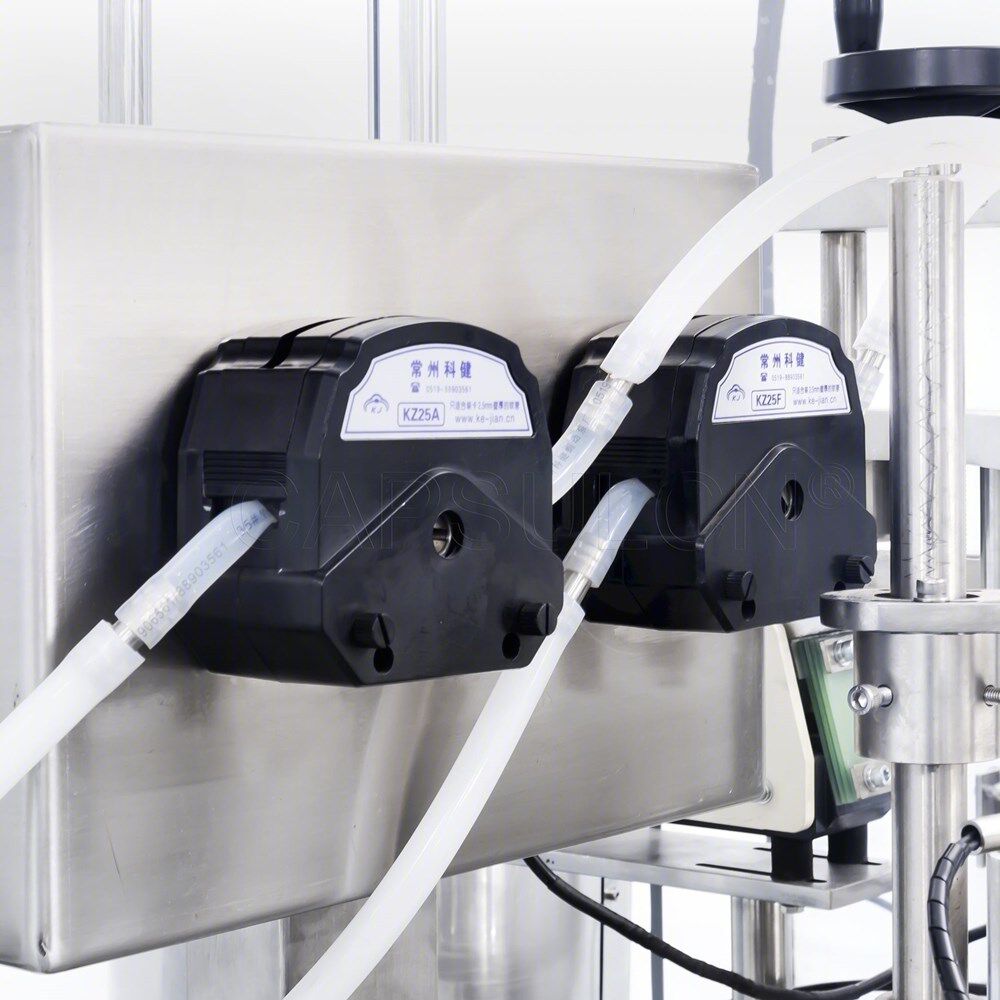
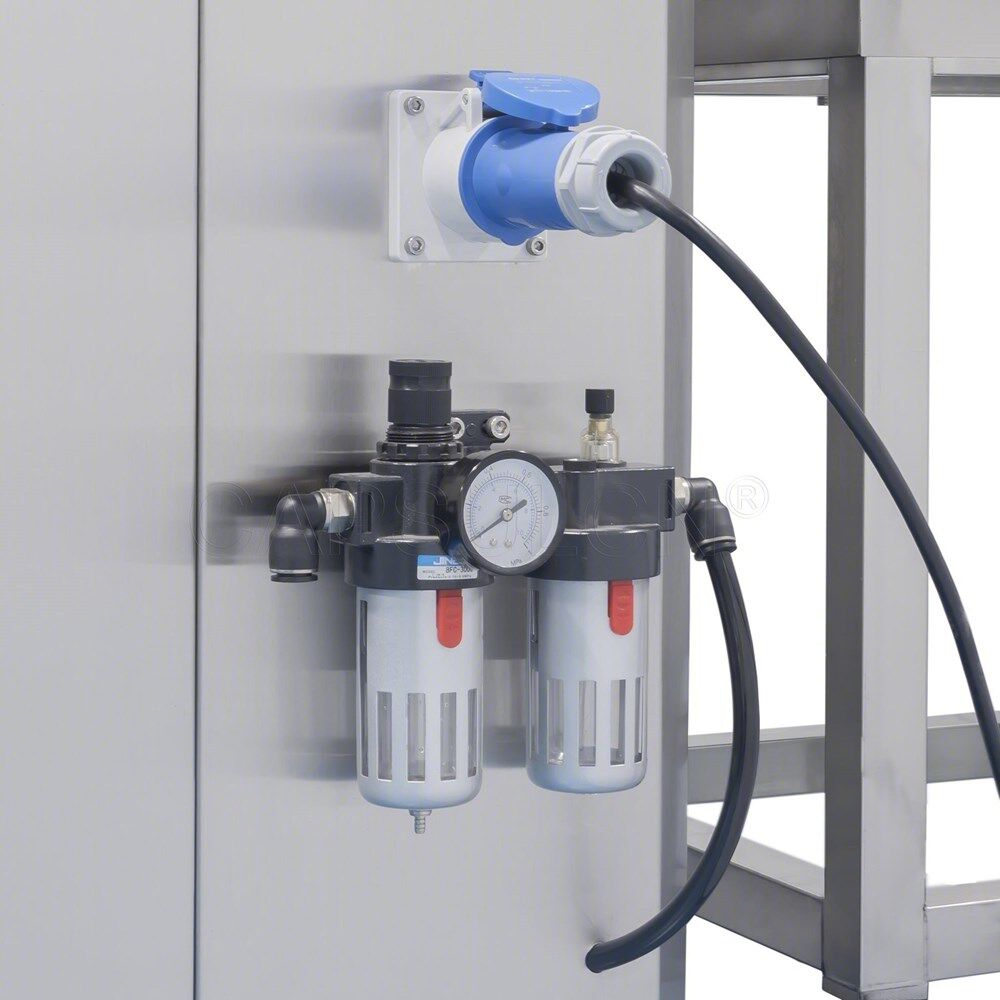
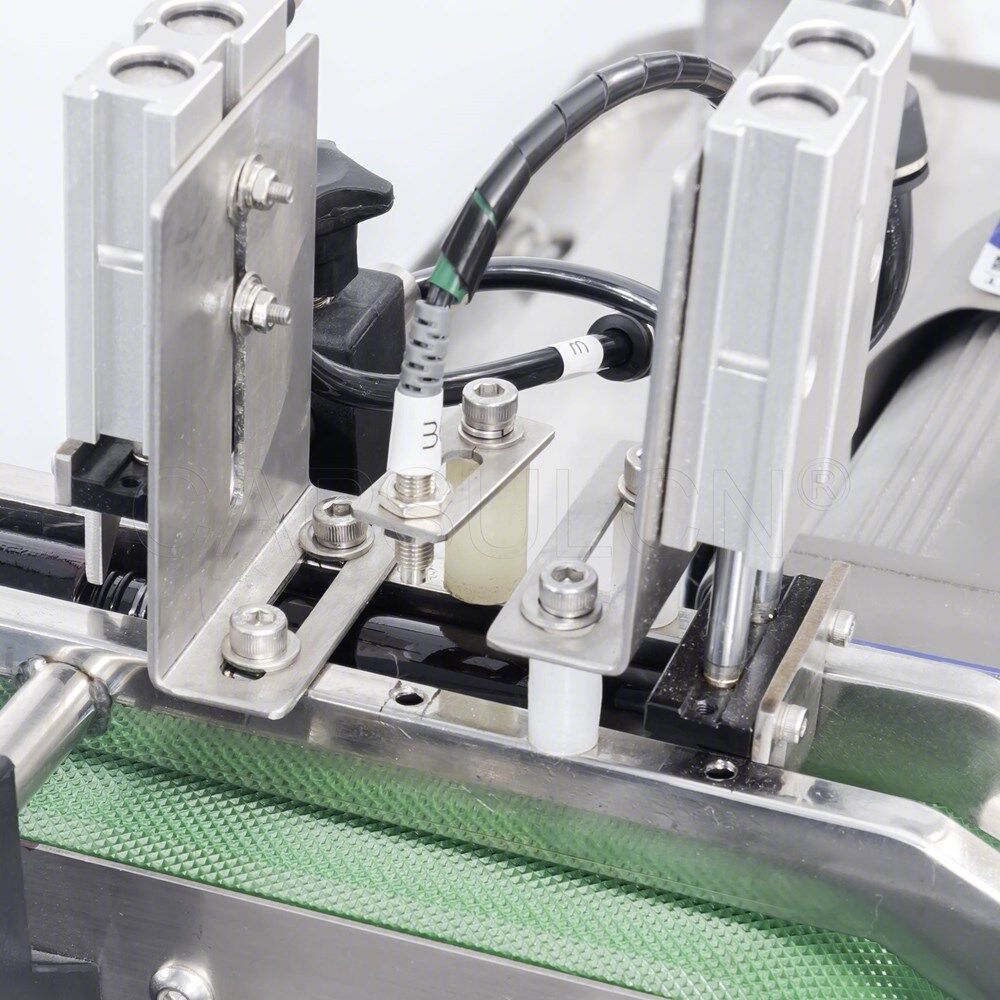
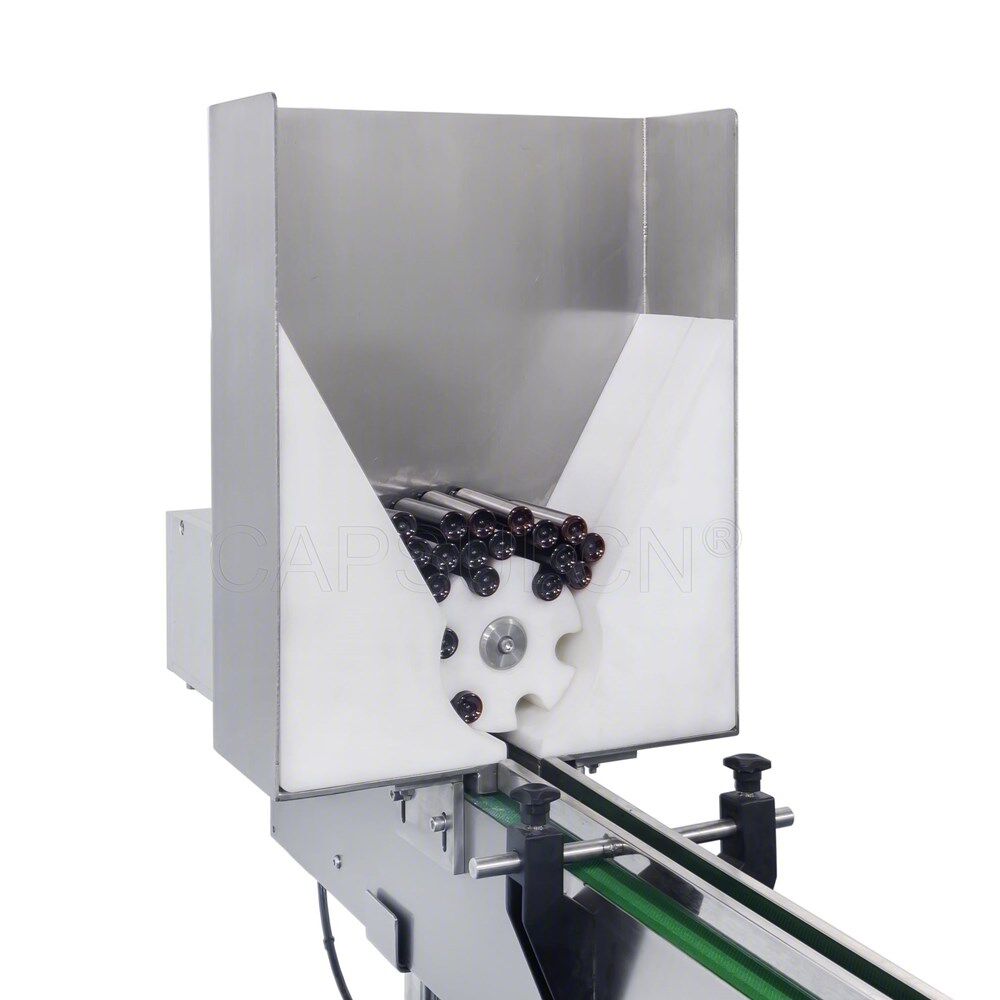
Introduction
This type of Bottle Filling& Cap Screwing Machine is suitable for filling bottles with various moderate dose. The machine has following features: b bottle-arranging and bottle-sending with rolls, and filling with Peristaltic pump in fixed position in the disc, cap-sending by vibration and cap screwing by rotating heads. The structure of the machine is compact and rational, and it can easily coordinate with other equipment to form a production line. The machine has been equipped with a protective cover consisting of PC board and 304 stainless steel frames.
Specifications
Model | CGS-1 |
---|---|
Production capacity | 1500-1800 bottles/hour |
Air Pressure | 0.5-0.8 MPa |
Air volume | 25-27m3/h |
Power Supply | 220V 50Hz |
Total Power | 2 kW |
Dimensions | 3500mm*2850mm*1750mm |
Weight | Approximately 800kg |
Main Parts
1. Bottle-arranging mechanism
2. Main rotary turntable
3. Peristaltic pump
4. Filling mechanism
5. Cap conveying and pressing mechanism
6.Capping mechanism
7. Electrical operation panel
Remark
- Check whether the lubrication state of each running part is good, whether the power supply is consistent, and whether the grounding wire is firmly connected to electricity in case of static electricity.
- Bearings, gear transmission parts, rotating and running swing parts, reciprocating shafts, and lifting shafts are needed to be filled with N68 mechanical oil twice a day. Cams need to be greased once every half a month, and the engine oil of cam indexers and gearboxes need to be changed every year.
- Check regularly and tighten the fasteners of each terminal. Regularly check whether the lead-out line of the distribution box is slack or not. Tighten the wire if it is slack in case of electric leakage due to mechanical friction Frequently check vulnerable parts, find damage, and replace them in time.
Write your own review
Also Offers




Our Team
As an expert in the pharmaceutical and pharmaceutical packaging industry, iPharMachine has provided solutions for hundreds of pharmaceutical and health product manufacturers for 17 years. By visiting customers, we get good reviews from our customers.
- info@ipharmachine.com
- English Español Deutsche